环氧贴片
有源光缆(AOC)组件
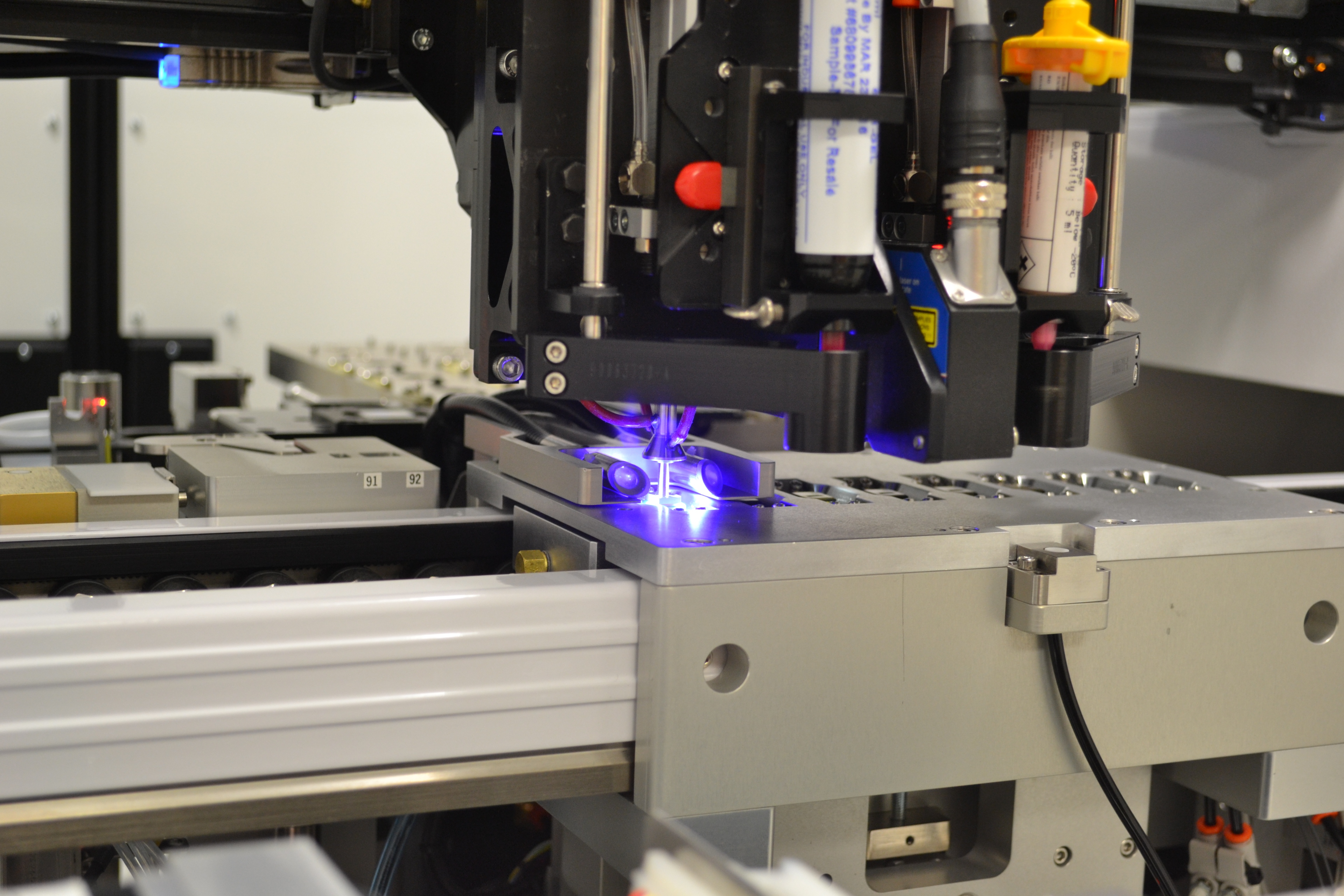
在线UV组装
最常见的环氧贴片粘结台由一个自动泵点胶系统组成,或者作为独立点胶台,或者作为环氧贴片系统的辅助功能。其他环氧贴片方法包括材料和丝网印刷的环氧冲压(与环氧冲压贴装有关)。粘合剂的属性因技术而异。点胶是环氧贴片的常见方法。
热耗散是环氧贴片需要考虑的另一个因素。对于大功率器件,在金属接触层可能需要驱散来源于功能型IC器件的高热量。在这种情况下,可能需要不同的贴片粘结工艺(共晶贴片)。
环氧贴片粘结材料点胶
一般来说,在环氧贴片粘结材料点胶过程中对用量的精确控制至关重要。所需精确度的级别影响所使用泵的类型。简易型气压泵以低成本针对合理的用量精度提供简单的机械方式。根据泵送的材料和所需的用量精度,正点胶泵和回转螺旋泵是所用的其他两种泵。常见一段式环氧系统通常具有较短的可用时间跨度(适用期)。在最终选择时还要考虑的维修级别与泵类型。
当选择适用于环氧贴片的粘合材料时,必须注意特定用途的热规格和导电规格,通常由终端IC模块的性能需求所驱动。与环氧贴片粘结材料供应商合作,工艺工程师可以针对环氧贴片的具体应用选择最合适的环氧材料。通常进行功能性试验以便确定最佳选择,一般需要权衡成本和性能、操作可重复性及可靠性级别。无论是配量、筛选,还是冲压,材料的黏性和颗粒大小是成功工艺的主要因素。
环氧贴片粘结材料冲压
说完了这些,还存在不使用点胶的环氧贴片应用。当贴片太小以至于贴片粘结材料的用量少于一般认为可靠的配量(例如,小型激光二极管),在这种情况下,就不使用点胶。
这种技术包括将环氧贴片粘结材料从槽里或从旋转传送盘中输送到基片上。通过表面张力差异进行材料输送。在最基本的配置中,将一个销浸入槽中。然后通过表面张力依靠销轴带走材料。当销 与基片接触时,通过表面张力再次释放材料。虽然该速度慢于点胶速度,但是用这种方法输送的量要小很多。可以将相同的传动机构应用于更复杂的工具,通常被称为环氧贴片粘结冲压工具。还可以使用转筒组件代替槽,以便在重新取回材料时更好地控制胶膜的厚度。
销传输和冲压的材料配方可能与点胶的配方有所差别。

环氧贴片
原位紫外线粘结
如上所述,以环氧贴片方式将贴片粘结到基片上之后,装配通常已固化,基于材料特异性热剖面进行交联。在贴片粘结固化过程中,贴片会移动。因此,固化后的元件位置会从最初贴装位置偏移到别处。这对于某些高级光电子应用来说是不可接受的。
对于光电子传输器件,容差十分严格,因此在装配过程中需要进行光信号的主动校准。因为成本较高,所以只有在其他方法无效时,才能使用此方法。在大多数应用中,被动校准元件是可以接受的,只要能够消除固化过程中的位置偏移即可。为了实现这一目的,必须在元件留在原位时对其进行固化。
这种“在工具中”固化方法被称为原位固化法。最常用的方法是使用紫外线能量将对紫外线敏感的环氧贴片粘结材料部分或全部固化,同时使用贴装工具将元件保留在原位。粘合剂固化后,就会防止元件进一步移动。
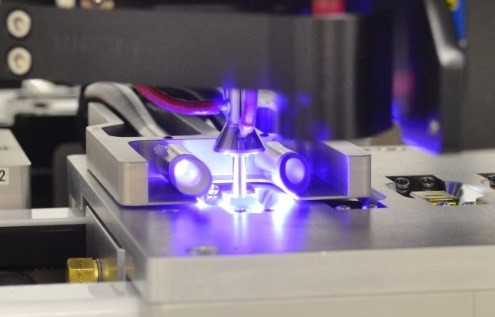
用于UV原位粘合的UV探针
对于此类应用,在MRSI贴片机上配置选配的紫外线固化套件(其中包括专业紫外线环氧点胶硬件和固化配件)。包括易清洗、时间精确/压力分配泵,适用于使用时间较短的材料;以及点胶头上的自动百叶窗遮光罩,用于防止点胶头因为过多的紫外线照射而堵塞。
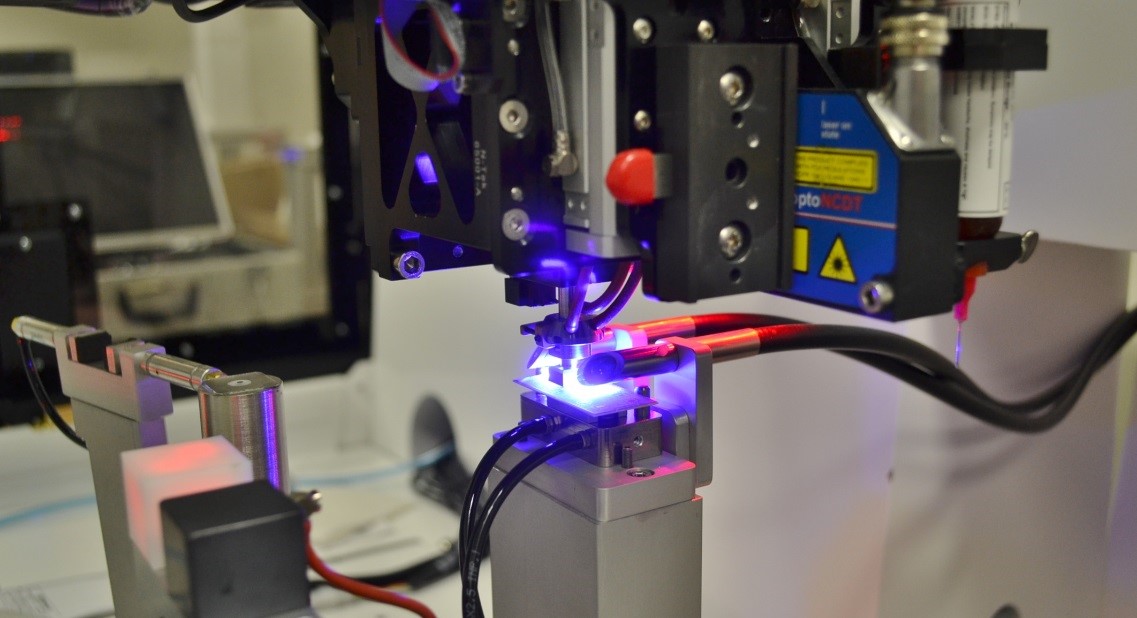
手动UV组装阶段